撰文/陳怡如
市場估計到 2035 年,電動車與燃油車的銷量將呈現黃金交叉,面對飛躍成長的電動車市場,在甫落幕的「臺北國際汽車零配件與車用電子展」中,工研院於經濟部技術處「臺灣車輛移動研發聯盟」(mTARC)主題館,展出最新的亮點技術,其中不乏與國際趨勢同步的產品應用,展現臺灣扎實的技術實力。
由經濟部技術處推動成立的 mTARC,涵蓋工研院等 9 個研發機構,2008 年起累積自駕車與電動車相關專利超過千件,可說是臺灣廠商打入電動車與自駕車產業鏈的彈藥庫,也是科技專案支援產業創新研發的成果。目前已授權專利廠商達百家、總計 257 件以上,協助廠商創造近千億的產值效益。
根據全球汽車產業市場(Marklines)資料顯示,2020 年電動車全球銷量已達 300 萬輛,成長率 46.3%,而全球車輛電子市場總值將近 3,600 億美元,臺灣過去 5 年車輛電子產業產值,每年均有 13% 的成長,2020 年創造了新臺幣 2,700 億元產值。如今資通訊大廠加入,發展可望如虎添翼,推估 2025 年產值將達 5,000 億至 6,000 億元。
臺灣首款車用碳化矽馬達驅控器
今年工研院展出許多亮點技術,其中又以臺灣首款車用「碳化矽馬達驅控器」最受矚目。該技術目前全球僅少數廠商與國際電動車大廠特斯拉(TESLA)開發成功,工研院機械所經理張欣宏解釋,「馬達驅控器」和「馬達」分別扮演不同角色,汽車電動化之後,電池提供直流電(DC),但馬達運轉卻靠交流電(AC),「要讓馬達動起來,中間要有橋梁,把 DC 轉 AC,這個橋梁就是馬達驅控器。」
碳化矽(SiC)是全球大力投入的新一代化合物半導體材料,擁有高切頻、高效率、耐高壓、耐高溫等特性,在車用電子的應用廣泛。此次工研院將碳化矽用於驅控器中的功率元件,就是因為在電動車應用上,馬達驅控器的電壓最高、功率最大,「碳化矽元件用在這種高壓、高流、高功率的零件上,最能展現優勢,可大幅減少驅控器重量與體積,」張欣宏說。
雖然碳化矽有先天的材料優勢,但仍有許多周邊設計需要互相搭配。首先,高切換頻率雖可減少切換損失、提升馬達控制效率,但也會衍生電磁干擾問題,因而要採取高頻抗雜訊的驅動電路設計;其次,因為更耐熱,散熱系統也要做更嚴謹的設計,工研院透過開發主動溫度估測補償技術,確保模組溫度。
透過整體的模組結構設計,碳化矽馬達驅控器的功率密度也有提升。一般馬達驅控器的功率密約在 20kW/L,工研院研發的碳化矽馬達驅控器卻擁有 40kW/L 的高功率密度,以及 99% 的高效率表現,有國際水準。
張欣宏指出,碳化矽功率模組技術門檻高,目前各國投入廠商不多,量產車款中僅特斯拉採用。工研院這項技術現正在實驗室測試平台階段,預計明年初進行實車測試,未來可應用於電動貨卡車或電動巴士,提供動力驅控器國產自主完整解決方案,為臺灣在電動車關鍵零組件市場,攻下一城。
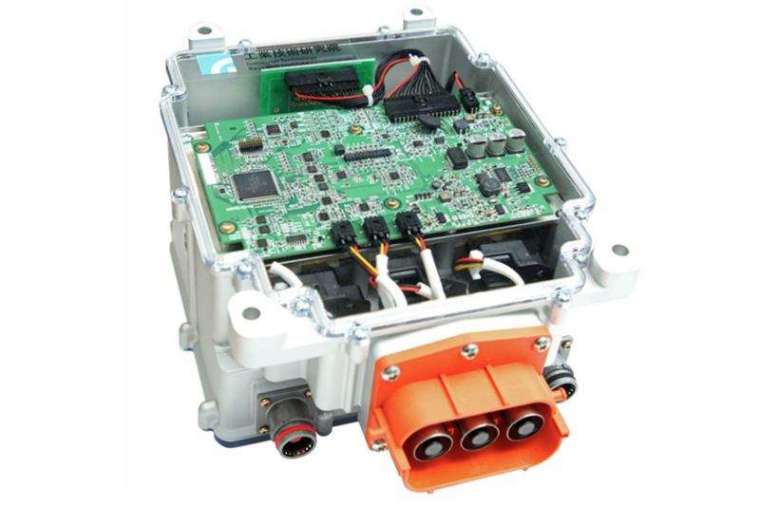
整合封裝技術 馬達驅控如四兩撥千斤
除了電動汽車外,工研院在電動機車的馬達驅控器上也有進展,發表全球首創高於 8kW 的高密度整合型功率模組。工研院電光所組長張道智表示,傳統馬達驅控器多採離散式元件,也就是一顆一顆單獨封裝好的 IC,最大缺點就是電路板體積難以縮小。以現行臺廠電動機車的馬達驅控器體積,馬達輸出功率大約落在 3kW 到 6kW 之間。
工研院採取整合方式,以半導體晶片的封裝技術,將更多晶片一體化整合在模組裡,過程需克服晶片位置、走線設計、均勻散熱等技術關卡,最終達到在相同體積下,可驅動的馬達功率超過 8kW 以上,是目前國內電動機車廠的 2 到 3 倍,相當於黃牌大型重機的輸出水準。
除了高密度整合型功率模組,整個馬達驅控系統還包含微控制板、電源板和驅動板等部分,這些電路板也透過整合式設計縮小體積,再透過 3D 堆疊結構組合,比起目前市面上的馬達驅動系統,體積可縮小三分之一。
張道智指出,這樣的設計也能解決使用者時時擔心車子沒電的「里程焦慮」。過往 DC 轉 AC,難免會有一些功率損失,一般馬達驅控系統的轉換效率約在 90%~92% 間,但工研院的整合式設計,電流路徑縮短,轉換效率可高達 97% 以上,有效提升電動機車續航力。先前工研院已接受國內電動機車業者的委託客製,預計下半年可出貨,近期也跟臺灣和日本馬達廠合作,有機會應用在大型電動重機上。
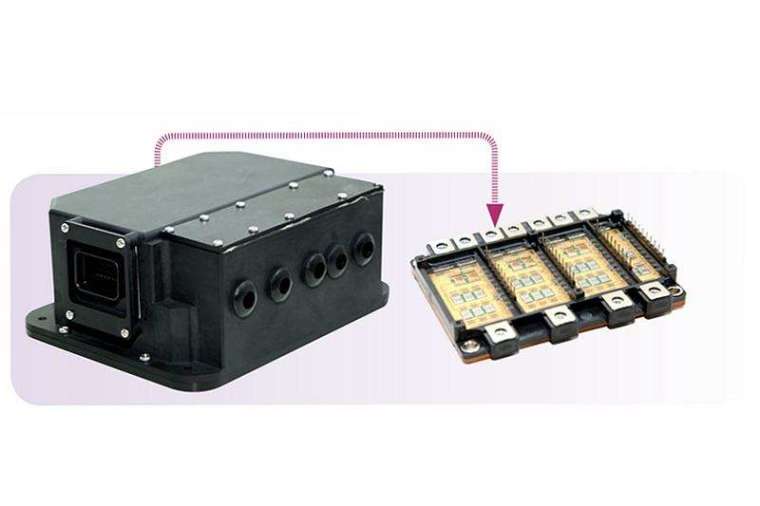
半導體打線技術為電池安全把關
電動車另一個關注焦點,是電池的安全問題。張道智表示,現行電動機車電池多採焊接技術,將銅片或鎳片以雷射點焊的方式,把電池芯一顆顆串接起來,一旦其中一個電池芯過熱開始燃燒後,無法產生保護機制,造成延燒狀況出現。
現行電動機車安規,對防止電池延燒的要求愈來愈嚴格,為了解決這個問題,工研院展出的「充電電池組」,以超音波打線技術(Ultrasonic Wire Bond)取代過往的點焊技術,可達到保護機制。
所謂的打線,是用鋁線取代銅片,藉由超音波高頻率震動,透過表面摩擦,達到牢固接合的效果,是半導體封裝的常見方式。張道智表示,選擇鋁線一是因為材料普及;二是因為鋁的熔點為 660 度,一旦電池開始過熱,就會達到鋁線熔斷的溫度,「鋁線可以扮演類似保險絲的角色,有效阻卻延燒。」
但鋁線粗細只有 250 微米,大約是 5 根頭髮的寬度,打線最大的技術門檻在於整體品質控制,精準控制超音波震動力道,每一條線都要打得力道均勻、恰到好處:太大力可能會把電池基礎打壞,打得過輕,接點強度又不夠。此外,也要設計鋁線的連接方式,才能讓電流均勻分布,「連接方式不同,電流走法不同,發熱的模式也不一樣,」張道智說。
目前臺灣投入此技術的廠商仍屬少數,工研院也已取得許多電池廠委託客製設計整個電池模組。未來除了電動機車,也可用於輕型電動車,如高爾夫球車上,布局輕型電動載具的電池商機。
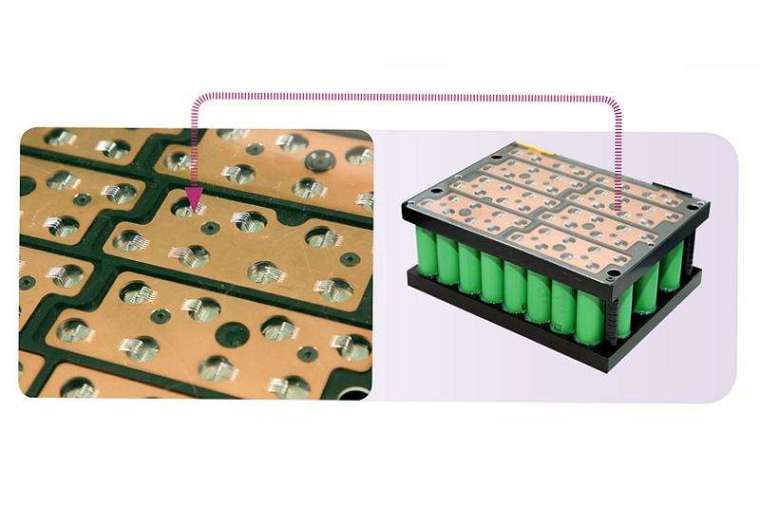
二速傳動模組有效提升續航力
突破電動車無須變速箱的迷思,工研院日前也發表,由經濟部技術處科專支持的「電動車傳動模組設計與多速換檔技術」,並協助齒輪大廠「本土股份有限公司」,開發臺灣首款自主設計製造的「電動車用二速傳動模組」,未來可運用於高性能的房轎車、休旅車及客貨兩用車上。
工研院機械與機電系統研究所所長胡竹生指出,觀察近年電動車發展趨勢,國際傳動大廠相繼投入研發二速傳動模組,並據此發展三合一動力系統,以提升整車加速性能與極速,並平衡電動車動力系統在高負載與高速時的能耗與動力表現。
相較於單速齒輪箱,二速傳動模組以兩檔位高低齒比,提升車輛加速與極速性能,可同時滿足電動車輛在高速與高負載狀態下的動力需求,並使馬達在兩種狀態下均能保持高效率的動力輸出,有效提升整車 10% 的續航里程。此外,二速系統可在維持相同性能的前提下,選用較小功率的馬達,達成動力系統小型化的目的,以此優勢切入高階電動車市場。
經濟部技術處科長張能凱表示,過去臺灣車輛傳動產業,以齒輪零組件生產代工為主,對模組系統設計較少著力,此次工研院與本土公司的合作,不僅補足國內在傳動模組設計、分析、驗證的技術能力,同時協助國內汽車零件製造廠轉型為系統模組廠。
此產品做為電動車三合一動力系統的基礎,也可整合國產化的馬達及驅控器資源,形成產業價值鏈,有機會打入國際電動車產業供應鏈,健全國內電動車動力系統產業。工研院多管齊下,率先投入臺灣電動載具產業需要的關鍵技術,布局市場空缺,取得電動車時代的致勝先機。
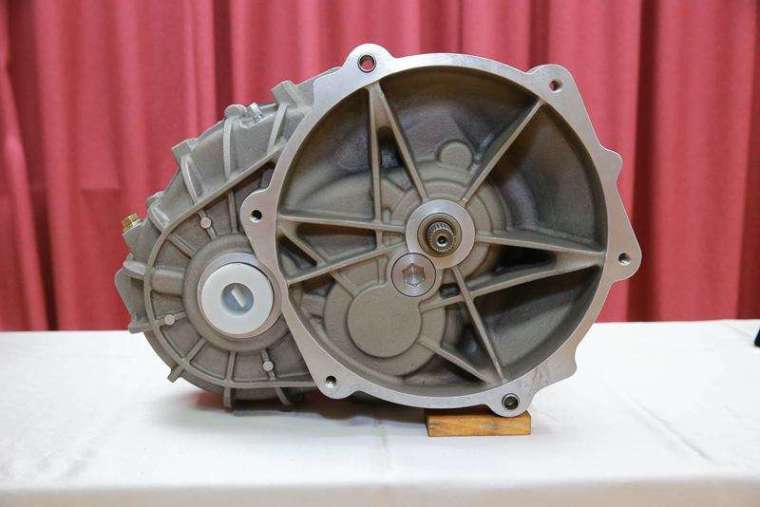
轉載自《工業技術與資訊》月刊第 351 期 2021 年 5 月號,未經授權不得轉載。