過往塑膠產業以人力檢測產品良窳,不僅耗時也浪費成本,塑膠射出成型設備大廠富強鑫攜手工研院,以「智慧感測成型平台」線上即時檢測製程,提升產業整體生產效益。
日常生活中塑膠用品無處不在,民生如鍋碗瓢盆用品,高科技如手機、筆記型電腦、汽車都有塑膠製品的蹤跡。這些塑膠用品大多倚賴射出成型機進行生產,而富強鑫,正是國內最大的塑膠射出成型機械設備製造廠。
塑膠產業雖然發展成熟、應用廣泛,但生產環境、塑粒品質、設備老化失效等變因長期以來困擾業者,影響量產過程中產品品質的穩定性。過去業者大多是定時以人力抽檢產品,如此做法卻無法保證每一件出廠產品的品質,因此工研院與富強鑫共同合作利用「模穴壓力感測器」,偵測熔體在模穴內流動行為的變化,以積極的預防性做法達到更強大的線上品質監控。
富強鑫研發經理林宗彥表示,富強鑫自 2010 年起啟動轉型,從原本單純的射出成型產品製造,開始協助客戶進行全方位技術資源整合,提供線上品質監控的解決方案。在 2012 年開發模穴感測訊號偵測技術,利用熔體在模具內流動壓力、溫度所形成的變化進行即時比對,進行監控製程品質及線上即時檢測。不過,早期模穴感測器價格高,不符合臺灣中小企業的使用效益,2015 年富強鑫與日本模穴感測器廠商策略合作,以高性價比的模穴感測器開始著手市場的技術應用推廣,累積模穴感測器在實務上的應用經驗。
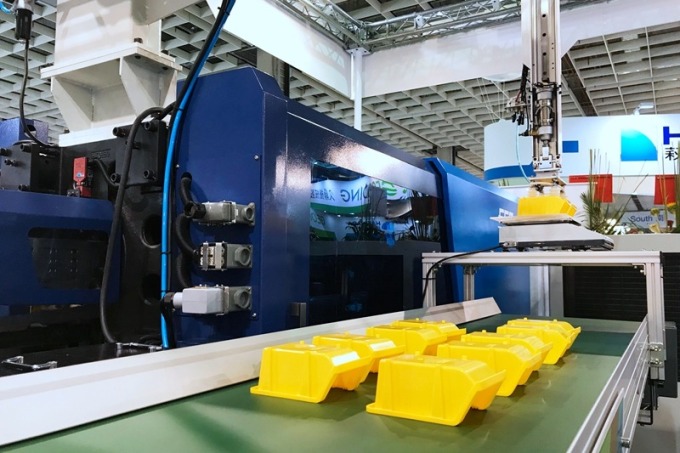
找上工研院 智慧再升級
當時工業 4.0 的概念還未在臺灣發酵,「研發過程中我們遇到最大的瓶頸,就是很多人不懂這是什麼樣的技術或該如何應用」林宗彥苦笑道。
富強鑫的強項在於機械設備的製造,「模穴感測器的運用原本並非既有研發團隊的專長,再加上 IT 技術的整合,等同於跨入完全不同領域的技術開發。」為此富強鑫找上擅長資通訊以及軟硬整合的工研院合作。
工研院將資訊系統技術(Information Technology;IT)與產業的操作技術(Operational Technology;OT)進行整合,開發「智慧感測成型平台」,這個平台可以把感測器所偵測到的參數以系統介面呈現,讓使用者可以透過螢幕了解機器運轉狀況、產品良窳、建構產品生產履歷,並提供建議解決方案,達到線上即時監控的目的,解決客戶長久以來所困擾的產線即時檢測問題。
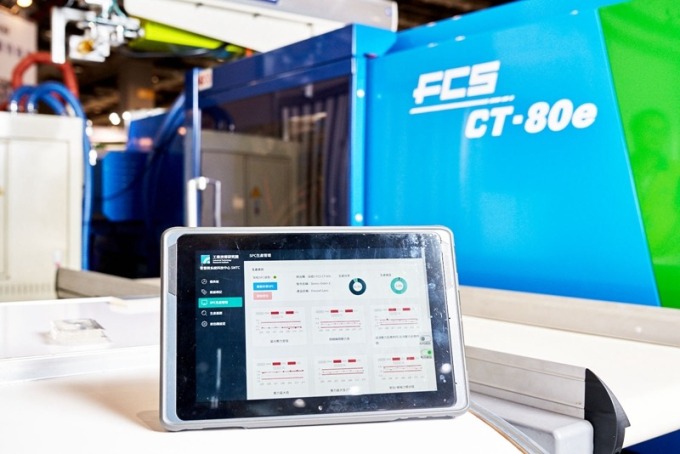
智慧感測平台上線 協同廠商導入運用
儘管智慧化的導入,有助提升生產效率,但初期的推廣並不是那麼順利。林宗彥回憶,4、5 年前,客戶對模穴壓力感測器的運用十分陌生,當時塑膠成型產業工業 4.0 的概念正在醞釀,對於加裝設備的成效也抱持懷疑的態度,因而裹足不前。為了敲開客戶的大門,林宗彥帶領富強鑫團隊,花費多年的時間進行工業 4.0 的教育推廣,舉凡舉辦技術研討會、協助客戶建立工業 4.0 團隊,希望讓新概念與技術的運用能在產業中落地生根。
歷經多年推廣,富強鑫終於敲開市場大門,與工研院合作的「智慧感測成型平台」在 2019 年正式上線後,富強鑫將協同廠商成為策略合作夥伴,共同導入技術運用,藉此觀察平台運用的成果,並隨時進行修正。「目前我們還在剛起步的階段,期待未來運作成熟後,可以再延伸至智慧塑機、智慧周邊、智慧製造、智慧管理的串聯運用,成為塑膠產業工業 4.0 的解決方案,全面提升產業競爭力,」林宗彥期待地表示。
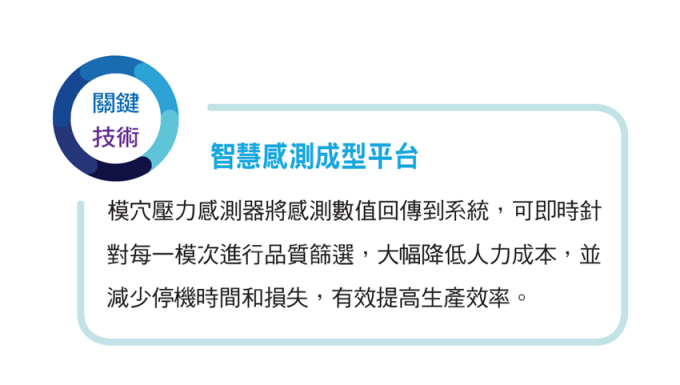
轉載自《工業技術與資訊》月刊第 337 期 2020 年 1 / 2 月號,未經授權不得轉載。